Over the course of the past twenty years, I have steadily reduced my reliance on paper items, eliminating checks, airline tickets, maps, personal calendars, pay stubs and files, freeing me to function with only a laptop and smart phone. And yet, many of the Quality Departments I work with, from various high-tech industries throughout the world, have not yet embraced new technologies. They still rely on inefficient manual paper systems to monitor the performance of their process. Why the avoidance of modernity?
In my role of assessing quality departments in industries ranging from biopharmaceutical to food manufacturers, there are several common factors that cause them to continue using cumbersome, manual quality management systems: a fear of regulatory compliance, the cost of installing/validating, the resource drain for maintaining the system and finally the lack of valued outputs. Although prevalent and consistent in many companies, these obstacles are not insurmountable.
Fear of Regulatory Compliance
Since the late 90’s, the dread of validating every software solution used in a company, including Word, have prevented Quality Departments from implementing electronic systems. As a quality auditor, I am often greeted with a pleasant smile when a Quality Director assures that validation does not need to be covered since they use manual systems. Even after finding numerous errors in manually created trend reports, Quality Personnel resist automated systems for the fear of a possible regulatory citation, which would be equivalent to a motorist deciding to walk for fear of getting a speeding ticket. In today’s market, there are diverse QMS software which are used in approved facilities.
Cost of Installing/Validating
As the Quality Department frets over potential regulatory risks, other departments fear the huge costs of validating complex QMS software. Collecting valuable resources for implementing QMS, paying various licensing fees, and establishing support groups are all areas that quickly add cost without assuring reciprocal value in return. These costs can run into hundreds of thousands of dollars. Added to the validation costs from the vendor are the internal costs to execute testing protocols. In reality, these costs can be controlled as there are QMS software systems where the costs are more manageable if you leverage validation provided through the vendor.
Resource Drain for Maintenance
The resource demand, although smaller after validation can remain high. Larger companies may have multiple IT personnel to perform daily system needs, such as granting access to a system, updating work flows and troubleshooting bugs. Unfortunately, many companies do not have these available resources. There are two steps to help from a maintenance standpoint. The he QMS software needs to be validated in such a way that allows the user group to operate with a validate space to allow for some flexibility.
Lack of Value
Some Quality Departments have avoided automated QMS software, while others have dismantled them. The most common reason I have witnessed has been the lack of value derived from the system. As in maintenance, some companies rely on an IT group to design reporting, alerts and other features. This creates expense as well as a reactive system. A modern QMS platform must allow the end user to be able to stratify their data to meet their specific quality metric needs in a dynamic way. If your Quality Department must contact IT to set up new reports, then attend months of meetings, it alienates a Quality Department from their own data. The eQMS system must also be structured to allow the exporting of data to be interfaced with other company systems such as purchasing and regulatory.
A bright future with eQMS
The proliferation of eQMS software, with vendors working to address the obstacles listed above, have allowed companies to approach implementation with greater optimism. It is not a magic bullet, but if a company selects the right software and designs in a practical way, many Quality Departments can move into the twenty-first century.
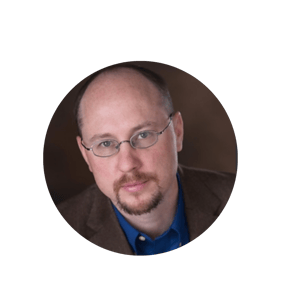